Pipe Clamps
G10 Micarta® can be very cost-effective insulation as compared to Polyurethane foam (PUF), especially for medium and large shoes. It offers tremendous benefits at various stages of a project, including but not limited to:
- Procurement
- Installation
- Handling, transportation, and storage
- Plant Maintenance
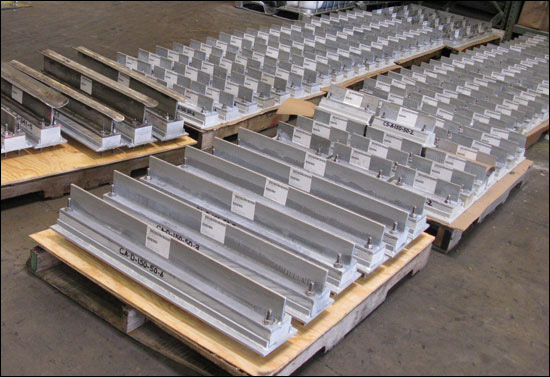
Major Advantage of G10 Micarta® Supports for Procurement
G10 Micarta® supports involve fewer steps to manufacture, allowing for a quicker fabrication turnaround. It takes 2-3 weeks less on average than PUF supports for delivery. This enables the ability to catch up on deadlines and reduce downtime.
- G10 Micarta® shoes cost less than PUF shoes of the same size, meaning Low Capital Expenses:
Advantages of G10 Micarta® Supports During Construction/Installation
G10 shoes can be sent to the pipe fabricator and can weld directly to the pipe spool, meaning there is minimal installation in the field. It takes 3-5 hours to install a PUF shoe in-field, depending on the size. G10 Micarta® shoes save that FIELD installation time.

Shop welding of G10 Micarta® shoes is much cheaper. As G10 shoes are weld to pipe spool at the fabricator’s shop, they can be inspected and tested in the shop; no inspection and testing in the field. More cost savings as inspection and testing is done at cheaper rates at pipe spool fabricator facilities rather than in the field.
As G10 Micarta® shoes are handled along with the pipe spools, there are fewer chances of missing supports in the field. Less OS&Ds to worry about for both the client and supplier.
Major Advantage of G10 Micarta® Supports while Handling, Transportation & Storage
G10 Micarta® supports are less fragile than PUF, making the handling, transportation, and storage of G10 to be trouble-free. No special packaging required, saving the time & the cost of special crating. Stronger G10 supports reduce the chances of accidental damage, thereby the need to re-fabricate the support.
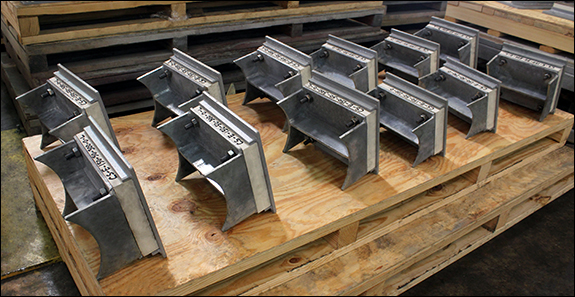
G10 Micarta® supports have insignificant water/moisture absorption rate, this means:
- No structural deterioration in adverse weather, especially in the wake of heavy rain and storms. PUF deteriorates in wet weather or humid climates
- Better life of the support
- Less maintenance and more saving
Testing of G10 Micarta® Support
![]() |
![]() |
![]() |
![]() |
![]() |
Comparison of G10 Micarta® vs. PUF from previous test reports:
![]() |
![]() |
Time-dependent temperature variations at the stated locations using G-10 Micarta®. (i) T-pipe; (ii) T-top; (iii) T- ambient; (iv) T-Bottom, (v) T-BOS. |
Time-dependent temperature variations at the stated locations using Polyurethane. (i) T-pipe; (ii) T-top; (iii) T- ambient; (iv) T-Bottom, (v) T-BOS. |